
Podcast: Demystifying Industrial Automation, With Dave Vasko
From bottle manufacturing to machine repair, automation has made just about every industry more efficient and adaptive to consumer demands. But despite its omnipresence, policymakers have failed to fully understand what drives industrial automation and why it matters for the economy. Rob sat down with Dave Vasko, director of advanced technology at Rockwell Automation, to discuss the latest trends in industrial automation—including innovations powered by artificial intelligence and virtual reality—and to consider how policymakers can spur manufacturing productivity and ensure the United States is globally competitive.
Mentioned
- Robert D. Atkinson and Daron Acemoglu debate: “Is the United States Tax System Favoring Excessive Automation?” (ITIF event, November 2020).
- Robert D. Atkinson, “Federal Statistical Needs for a National Advanced Industry and Technology Strategy” (ITIF, July 2021).
- Stephen J. Ezell, “Why Manufacturing Digitalization Matters and How Countries Are Supporting It” (ITIF, April 2018).
- Lawrence Summers and Alan Auerbach, “The Investment Tax Credit: An Evaluation” (National Bureau of Economic Research, November 1979).
Related
- Robert D. Atkinson, “10 Types of Work to Automate or Move Online for a COVID-19 World” (ITIF, July 2020).
- Robert D. Atkinson, “The Enterprise Automation Imperative—Why Modern Societies Will Need All the Productivity They Can Get” (ITIF, November 2019).
- Robert D. Atkinson, “How MIT’s ‘Work of the Future’ Project Gets It Wrong: Raising Taxes on Machinery and Software Would Kill Jobs and Hamper Wage Growth” (ITIF, 2020).
Auto-Transcript
Rob Atkinson: Welcome to Innovation Files. I’m Rob Atkinson, founder and president of the Information Technology and Innovation Foundation. We’re a DC-based think tank that works on technology policy.
Normally you’d hear Jackie Whisman say that we’re the world’s top-ranked think tank for science and technology policy. But unfortunately, we had a massive storm yesterday in DC and her power is out. So it’s just me today, but we have a great guest, so we’re really looking forward to a great conversation today.
Our guest is Dave Vasko, he’s the director of advanced technology at Rockwell Automation, where he’s responsible for the development of advanced technology to realize the future of industrial automation. He serves on the NIST Visiting Committee on Advanced Technology, and he’s on the board of the 5 Lakes Institute and is a member of the Forbes Technology Council. Dave also holds 77 patents, which is really amazing in industrial automation. For those of you who don’t know Rockwell Automation, they’re the leading, one of the leading automation and industrial systems companies in the world. They’re headquartered in Milwaukee, Wisconsin. So Dave, thank you so much for joining us.
Dave Vasko: Rob, thank you. It’s an honor to be here today.
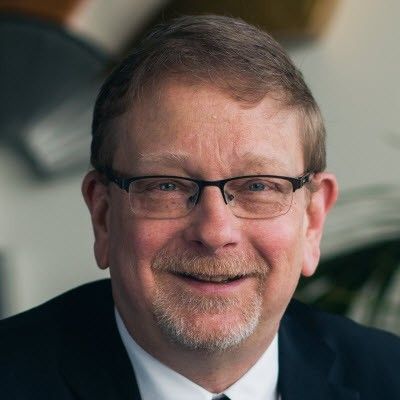
Rob Atkinson: So before we get into the whole question of automation, which is clearly a huge issue, and there’s a lot of, I think, misunderstanding about it. Particularly in Washington and really all around the world with, I think, policymakers. Can you tell us a little bit about Rockwell and what your role is there?
Dave Vasko: So Rockwell Automation is the largest company dedicated solely to industrial automation information. We’ve had the honor of serving our customers since 1903. You may not know our products, but we like to say by the time you arrive at work in the morning or having your first cup of coffee, you probably have experienced four or five of the things we’ve helped make. Be it coffee or beverages or food or petroleum or automobiles. So we’re really part of people’s lives. I feel that really the honor of being at Rockwell, for 36 years, I’m responsible for applied R&D, global standards and engagement and innovations institutes. So we get to try out the technologies that are emerging and see how they can be applied in the industrial space and really to bridge those gaps to apply those technologies.
Rob Atkinson: Yes. You know, in the innovation ecosystem or literature or policy, oftentimes people focus on product innovation. They’re, oh, I’m waiting for the iPhone 15 or it’s going to be a new drug and that’s super important, no doubt about it. But oftentimes we lose sight of the importance of what’s called process innovation, how we make things. There’s been an enormous amount of innovation there since Rockwell started and a lot of it from Rockwell. Tell me a little bit about what is process innovation? Why should we care about it? Why should a policymaker care about it?
Dave Vasko: Oh, absolutely. So that’s what really allows our products to be competitive. By working on the process, to make things more productive, be able to produce more product, to be able to control the quality of that product, to be able to integrate the supply chain, to ensure there’s resiliency in actually producing the product. That’s crucial. That’s where the prices of the end products come down, the availability goes up, people can afford those things. So that’s really crucial to the economy and it’s crucial to the job creation.
Rob Atkinson: You know, I’m going to sound like a total wonk here, which I am. But one of the favorite things I do when I’m on vacation is I try to find places where they’ll give you a free tour of a factory. I’ve visited a Ford Motor Company factory. I visited a teddy bear factory in Vermont. That was cool. I visited the Phillip Morris factory. You can say you don’t like cigarettes or like them, but I got to tell you the way they make cigarettes is pretty cool.
I visited a factory in Italy a couple of years ago. What was striking about it was it wasn’t a big, giant factory, it was a midsize company. What they actually made were electromechanical switches that are on appliances and dishwashers and all of these things. What was really interesting about it though, was that they had worked with their local technical college and one of the professors there. All of the employees were now wearing apple watches and they had used what’s called the Internet of Things and WiFi and all. They could really tap into machines in real time if a machine was slightly off. They told me like, machines have tolerances and if it goes out of tolerance, you can have a run that’s just, you’d have to throw it away. They said, they would look at machines at the end of every day. Now, in real time, they know exactly what’s going on. Anyway, that’s this whole thing of what people talk about smart manufacturing or Europeans call it industry 4.0, can you lay that out for us a little bit? What is all that all about?
Dave Vasko: Yes. So you’re right. It’s really about changing the pace. So I’ll be honest. I’ve seen a mining application where they do a mining plan once a year. You think about all the things that can change in a mine within a year. You’d love to be able to do that every day. That’s really where it’s going to be, do it every day or do it in real time. When somebody is going to align it, look at what’s happening, what you’re producing, how to optimize and make sure the quality is where it needs to be. Because you don’t want to be sitting there producing scrap all day. Worst case you don’t want to be producing something that could get out to your customers and then have bad quality and have to pull it back in. So that’s really where the focus is, to be able to monitor those things in real time, to really give the people on the production floor, additional powers to be able to find what those problems are, to optimize things, to keep the quality where it should be.
Rob Atkinson: My colleague Steven Ezell at ITIF has really done a lot of work on this whole question of smart manufacturing and what are the policy questions. People were talking about this since the year 2000, 2010. But it’s really only in recent years where you have sensors that are cheap enough, you’ve got wireless systems that can communicate, you’ve got software systems. So it was really now machines talking to each other and machines talking to people that enable this to happen. We always had, well, I shouldn’t say always, but with the rise of what are called CNC machines, computer numerically controlled machine tools, those are a big improvement over the old kind where a worker had to set them up. But now we’re in a whole new level where the machines are connected and what’s that all about, why is that important?
Dave Vasko: Yes, you’re seeing that the production between machines. We’ve had productive machines in the past. Now you’re seeing more and more of the machines connected. You’re right, that we have been talking about this, really, since the year 2000. We’ve been looking at how this is going to change industry and the technologies really have risen up that allow that to happen. But by machines interconnecting amongst themselves, they can then operate together. They can optimize together, come up with the best operation. Some of this is not intuitive, you may slow down one machine in order to speed up the entire line. Without a system view, you wouldn’t have been able to see that in the past.
Rob Atkinson: That leads into another component, which we haven’t talked about and that’s software and AI. I know we had a conversation a while ago, Dave I remember it. But I was really intrigued by what you had said was that you’re working with your customers to develop AI. That’s sort of easier to handle, that you don’t need to be some computer scientist in Silicon Valley to manage this. Can you say a little bit about the role of sort of intelligence and AI in these? Then also about the, I don’t know, lower skill or moderate skill AI that’s being rolled out?
Dave Vasko: That’s really the key. Be able to have people with domain knowledge, make the decisions and apply to AI. If it’s just Ph.D. data scientists, it’s not going to have much applicability. We don’t have enough people trained and it’s going to be too expensive to apply. So what the AI methods have been trying to do is be able to recognize patterns and create the groupings of those patterns and then use the domain experts to make decisions about what that is. You have number of groupings, okay, these groupings represent a quality product operating correctly. These groupings represent a particular problem you may be facing. The people on the floors, the people that are experts are the people at the main or at that machine, or even the operator are the ones that understand that the best, they could provide the insight. That would have taken a huge amount of time by data scientists to understand. So that’s really leveraging the human processing power of those people to be able to give them superpowers and give them an augmentation of what they’re doing.
Rob Atkinson: This is a little bit like what people call AI as an enabler. People talk about, for example, that radiologist might get put out of business by AI. I don’t really believe that. What AI does for an expert radiologist is it gives him or her an extra set of tools to complement their own insights and skills. That sounds like what’s happening here on the shop floor. A skilled worker now has a tool essentially, and they help with the tool and the tool helps with them.
Dave Vasko: Absolutely, absolutely. It also jumpstarts people coming in, we’re having a lot of new people coming in. In factories, we’re seeing some of those experienced people leaving and it typically takes years and years to gain experience. But if we can give people insights into what they’re doing that would have taken 10 years to develop, if they could have those insights coming in the environment and being able to provide them with additional help, that jump starts their careers and their impact on the organization immediately.
Rob Atkinson: I want to go on one little side road here just for a moment. We have a new initiative on XR, essentially virtual reality, augmented reality and really looking at the promise of that in a whole set of areas, healthcare, education, and all. But I’ve heard that you can use XR, VR like a Microsoft HoloLens, for example, to help newer workers or existing workers really be able to understand things that might take them a longer time to understand. Is that something you see as well?
Dave Vasko: Oh yes, absolutely. There’s a lot of uses for that. So we’re using VR to actually construct plants before they’re ever built. We can then train workers in how to interact with the plant. We also can pilot the operation of the plant. We can put simulation tools behind the plant. We can do optimizations in the plant. We could see workflows. That may be a problem, that you have restrictions there. So you maybe leave a little more room for operators to get in there and work. So we could do all that ahead of time and train those people. Particularly in operations that maybe a little bit dangerous or require a lot of skill, you want to try them ahead of time. You want to get good at them before you’re ever in a situation where you needed to do that.
Then when we get into the operational phases, you think about somebody going out on a plant floor. If they have a HoloLens or AR headset, they can go out there and they can have an expert in their ear, seeing what they’re seeing, helping them to troubleshoot that. We could have that expert, we could push down a video to them. We could push down information about that equipment, maybe a checklist, if it’s something they only do occasionally and what they need to do for that particular operation. So that really helps the users. Instead of sending somebody to a plant to actually check something out, we can just have somebody to the HoloLens headset that is already familiar with the safety operations of that plant walk through and do those operations. That just speeds things up.
Rob Atkinson: Plus I would assume it also gives that operator more knowledge, more experience. Perhaps the next time he or she could maybe do it more on their own?
Dave Vasko: Absolutely, absolutely. It gives them that experience and they’re able to learn that. With so much of things rolling out, it allows them to really get the training many times just in time. So they’re not having to look through all these scenarios that could occur, but they can get the training they need right when they need it.
Rob Atkinson: You know, one question we hear a lot about, there’s an economist at MIT that I’ve had a debate with. Daron Acemoglu, who has, I think a very, I don’t know, to me, not very accurate or helpful notion of that, there’s good automation and bad automation. He’s been very critical of automation and robots. Our take at ITIF is all automation is good and there are going to be some processes where you can just automate it and you can have fewer labor hours to produce something. They’re going to be other systems though, where you’re using automation or robotics to either complement the worker or to do things you couldn’t do. I know we talked once about, I think it was the BMW plant in Germany that was using these smart systems, robotics, et cetera. But they were doing it in a way to basically increase their product flexibility dramatically. Can you talk a little bit about how that all plays out?
Dave Vasko: Sure. So that’s the one thing. I mean, humans have the ability to be, to really react and be able to do things very flexibly. Robots and automation have the ability to do repeatable operations. So you want to use the best of both. So you’ll see operations where you may use maybe using cobots to be able to learn things very quickly. The humans teach them to do that. They’re able to do those repetitive operations and the humans are able to take up the slack in between. But that working together is crucial and that productivity and having that flexibility to be able to react to those changes in demand are crucial.
Rob Atkinson: We see that right now, for example, with some of the supply chain vulnerabilities and some of that, not all of it. Some of it is just your system has committed to produce a certain kind of thing, and it takes a while to shift. Some of these new technologies, including cobots can make those shifts much easier to, oh, you see, demand is going to go this way, you can quickly shift over and meet that demand.
Dave Vasko: Yes, we’ve seen that a lot over the past 18 months. That benefactors are asking for more flexibility, particularly maybe the unpackaging. Like a food processor that was geared more towards the restaurants found that that market was drying up. Where the consumer market was just going gangbusters. If their manufacturing line was restricted to only producing, say 20 pound bags of french fries, they didn’t have a market anymore. They’d found that they were running three shifts and could meet demand for the consumer market. So we’ve seen more flexibility in how they approach that. And that the flexibility wasn’t always valued. I think people are seeing the need for it now, even to the pivot to things they do think they could even do in the past. We’ve seen people do that.
Rob Atkinson: That’s really interesting. Yes. We all experienced that with toilet paper early on in the, I actually remember I went online, I think Office Depot or Staples or whatever. I bought like four boxes of office toilet paper because that was the only toilet paper you can get. And hey, I got toilet paper because you couldn’t buy the small rolls so I got these big giant roles. But if we had flexibility, I wouldn’t have done that.
Dave Vasko: Yes. That’s true. They were having trouble selling those.
Rob Atkinson: Yes.
Dave Vasko: They’re having trouble selling those, yes.
Rob Atkinson: Yes.
Dave Vasko: It’s a great example.
Rob Atkinson: I want to jump into some of the policy questions. But before I do that, we have a new, well, probably the piece will be up by the time our podcast is out. But we’ve been looking at US productivity growth in manufacturing and using the Bureau of Labor Statistics numbers. What’s really striking is if you go from say 1998 to 2008 or so, what you saw was about a 40% increase in productivity. Then if you take that next 10-year period through 2019, you actually saw a slight decline in productivity. So, 10 years without real productivity gains. Now some of that could be mismeasurement. Some of it could be that it’s just super hard to be more productive because we’ve made factories so productive. But part of it might be also that these new technologies, that Rockwell’s piloting and other companies, are not quite there yet being they’re still early in adoption. A lot of the kinks and the bugs are being worked out. People still need to know how to use them. What’s your take on all of that? You think that’s a reasonable hypothesis?
Dave Vasko: I think that is, I think that’s on the right track. So I think, maybe we did pick the low hanging fruit. But I’ll be honest, we’re bringing some pretty big ladders into the orchard right now. So you look at the technologies that are rolling in. Really the widespread industrial networks and be it wired or wireless that are coming into the factories. We’re still early on that. I think we’re doing very well, particularly with some of the cellular networks outside. Those are going to migrate more inside on premise networks. Those are going to provide increased connectivity within the factories. That’s going to help resurgence really in AI and machine learning. Particularly some of the most difficult applications around vision and natural language processing are being solved.
But there’s still a problem applying those. We’re getting to the point where making easier and easier for people to apply it, it isn’t quite there yet. But for many applications, it is, and people get more experience that it’s going to help. We’ve seen significant advantages in the processing in either cloud or at the edge that really allow these things to happen. Then the whole thing with the XR technologies that we talked about and things like digital twin. So these technologies are rolling in and we expect to see pretty significant increases in productivity from that, in reduction of downtime and improvements in quality around those things.
Rob Atkinson: That’s really interesting you mentioned digital twins. I was in Italy about a year and a half ago, or maybe longer. I visited this company and it was the coolest company. What they made were machines that Dasani and all the water bottle companies use. They basically had two main machines, one that made the little caps and one that made the bottle. I talked to the chief engineer and he said that the tolerance, I can’t remember what, it was like four microns or something. I mean, it was just like smaller than a hair. He showed me the machine that makes the caps. What they do is the worker pours in these plastic pellets at one end and about 20 feet down the way, outcomes I think a million caps a day. I mean mind-blowing.
But I was talking to the engineer about that and he said, one of the things that they’re doing is they’re developing digital twins for all their customers. That gives them the ability to monitor these machines, maximize output or efficiency. I thought that’s really, really interesting that notion of a digital twin, where you have the sort of the same machine, but in digital, and then you can monitor it for improvements. Also learn from the machines, that seems quite new.
Dave Vasko: Yes. That’s a really good way to apply digital twins. On machine basis, to be able to monitor the machine, to see how it wears, where things are going to change. Actually, digital twins have been around for a long time, but it does take some work to get there. That’s what really has limited the adoption. So we’re seeing more adoption. First it was applied was even over 20 years ago, applying a digital twin in a factory. It was actually a case where there’ll be wear in the line and it was a steel mill. They would have problems when they switched from one product to another product. They could lose up to 10 tons of steel. So they’d have to kind of tweak in the parameters. The operator would have to tweak the parameters every time and they could change up to two dozen times per day.
So what we did, we created a digital twin of this steel mill and we learned where everything was, where the machines were, the tolerances, where, where the wear was occurring. So when new product came up, we would make the adjustments based upon that wear. Instead of losing 10 pounds of steel, we never lost a gram. We were able to hit every time, us spot on with what was planned. One of the side-effects was, we could have things that were broken in the plant and we’d be able to say, yes, you could produce it or no, you wouldn’t and we can make adjustments. So even with broken equipment, there’s still many of the products they could still produce. So I think that’s a great example. I do love the bottling. I’ve been to those manufacturers for the machines. It’s just amazing what they’re able to do. I love the measurements. We visited one with 14 different measurements for volume, because depending on what you’re making, you’re filling it with water or cognac, you really want a little different accuracy with that.
Rob Atkinson: Yes. Yes, exactly. Exactly. I don’t know. Water’s pretty valuable these days.
Dave Vasko: Yes.
Rob Atkinson: So Dave, just switching over now for the last few minutes about policy. Now we could talk for a long, long time about manufacturing policy. There does seem to be a resurgence of interest in it. The Biden administration with Build Back Better. They’ve proposed a new initiatives. You’ve got the Senate what’s called USICA, the US innovation and competition act. There’s a number of important manufacturing and applied R&D components there. What do you think are a couple of things that the federal government needs to do in the manufacturing space to make sure the US is globally competitive and more productive?
Dave Vasko: Yes. So I think there’s, we need to bring the small and medium manufacturers along. I’m not saying we forget that the big manufacturers, but we need to make sure the small, medium manufacturers are able to adopt the technology. They don’t have the R&D groups, they may not even have an IT team. They probably don’t have a security person. So we need to give them the tools they need to sort through the technologies and be able to apply those. Things like the manufacturing extension partnership that the NIST helps to run, which actually helps small and medium manufacturers learn those things. Manufacturing USA, actually looking at those challenging problems, doing the pilots with manufacturers to help them get them along and apply these technologies, that’s really so important to being able to move these things along and make our manufacturers more productive.
Rob Atkinson: Absolutely. We could not agree more. My colleague Steven Ezell wrote a report for NIST a number of years ago, where we benchmark the US MEP program against our competitors. While MEP is a fantastic program, one of the key things we learned was that our competitors are investing significantly more in those kinds of programs, as a share of their economy. The Japanese invest 40 times more, four zero. The Germans 20 times more. So I’m really glad to see that they have the proposals to significantly increase the MEP, hopefully they’ll go through. Same thing on Manufacturing USA. This was an initiative that we helped push in the Obama administration. The Chinese looked at it and they said, we want to do that too. They now have 15 centers, they want to go to 45 or 50. But their funding is an order of magnitude higher than ours. They’re putting big, big bucks behind. These are big, big Yuan’s I should say, behind this. Thoughts on if we expand Manufacturing USA, how that should work?
Dave Vasko: Yes. So we are seeing increases in the funding. I think that’s good. The one thing we’re seeing too is that some of those are being funded through the Department of Commerce. So the nimble was funded through Department of Commerce. There’s two more that look likely to come from the Department of Commerce. So I think that’s good. It’s probably more resilient as far as the funding coming directly from Commerce. So I like that approach. Yes. I think we can make some big investments. I mean manufacturing sector partnership was always frustrating to me because the payback, return of investment was so high. We received more tax dollars back than the investment. So it was one of those things, why don’t we double it? Why don’t we quadruple it? Why don’t we put 10 times more into that to really get more people adopting these technologies. We’re going to need it, we’re going to need it. It’s not just a small and medium, the large manufacturers need that ecosystem if they’re going to thrive.
Rob Atkinson: Yes. I mean case in point, we did an event recently the White House asked us to host on the new Biden supply chain report. Which if listeners haven’t listened to it, it’s a fantastic report—haven’t read it. They looked at four industries, including semiconductors and biotech and drugs, but small and medium-sized manufacturers are the key thing for the US supply chain health. If you don’t have that, you get OEMs, bigger manufacturers ended up oftentimes going offshore because they don’t have the supply chains here. So yes, I couldn’t agree with you more that that’s something we’ve got to really focus on.
So maybe one last question, Dave, and that’s a tax policy. So we had in the US for many, many, many decades, we had an investment tax credit. My favorite story of that was back in the early eighties, Larry Summers, the well-known economist. He wrote an article for the National Bureau of Economic Research, and it was an evaluation of the investment tax credit. What he found in that, he ran this big model, economic model. What he found is that, if you have the investment tax credit, you get more investment, no surprise, you get more productivity and you get a bigger GDP. So what was his conclusion? Get rid of the investment tax credit because it raised interest rates, just a tad. Because there was so much demand for capital now that it raised interest rates a bit. That meant there were fewer, like a teeny fewer housing starts.
So Larry Summers said we can’t have an industrial policy like that. We should have more housing. Congress eliminated the investment tax credit. Guess what happened? Investment, particularly in machines systems went down. Now in the 2008 tax bill Congress, you can argue elected or not. But I thought the main thing that they did, that was good and on the business side was they allowed companies to expense in the first year, their expenditures on equipment and machines. Before that they had to write them off over five or even 10 or 15 years. Now they can write them off. That’s due to expire. I believe at the end of this year or next year, I should get my numbers right. But it’s due to expire. It was a five-year provision and we’re very supportive of expanding, extending that. What are your thoughts on that in terms of the tax incentives or decisions that companies make? How does that play out?
Dave Vasko: Yes, I think that’s an important program. I think I love looking at the timeframe. Because you look at manufacturing and many people think about it as 5, 10, 15, 20 year investments. But if you want to grow, if you want to be competitive, you have to do it on a shorter horizon and be able to take advantage of those investments and write those off within the first year allows you to be more nimble and to have the flexibility that we really need to be able to be competitive worldwide. So, yes, we think that’s very important.
Rob Atkinson: Yes. In a lot of other countries, again, they don’t just do expensing, which is nice. They actually go further than that and they’ll do a credit. Our competitors really get that. So Dave, this is really fantastic. I’d love to keep going, but we have a time limit on these. So I really want to thank you so much for being with us.
Dave Vasko: Rob, thank you so much. It’s always a pleasure talking with you and really appreciate everything you do to really bring this information to people. What’s actually happening in the industry.
Rob Atkinson: Thank you. That’s it for this week. If you like the show, please be sure to rate us and subscribe. Feel free to email, show ideas or questions to [email protected]. You can find the show notes and sign up for our weekly email newsletter on our website, itif.org.
You can follow us on Twitter, Facebook and LinkedIn, @ITIFdc. We have more episodes and great guests lined up, new episodes will drop every other Monday. So we hope you’ll continue to tune in.